In today's evolving manufacturing landscape, the focus on ensuring product quality has led to a significant shift towards the verification of critical functional features during the production process. The rationale behind this trend is driven by customer demands, the imperative of cost savings through defect reduction, and a commitment to delivering consistent, high-quality products. One prime example of such a crucial functional feature is the rotating torque in pivoting joint assemblies. The need for in-process verification of this feature underscores its significance in the manufacturing process.
Constructing a pivot joint testing machine involves a multifaceted approach that demands careful consideration. Whether you're conceptualizing and designing the machine in-house or evaluating options from external suppliers, a comprehensive understanding of the intricacies surrounding pivot joint testing machines is imperative. In this article, we delve into critical factors that deserve attention, encompassing essential components of the machine's configuration, pivotal aspects of part fixturing, key considerations for gauging and machine verification, and the pivotal role of control methodology.
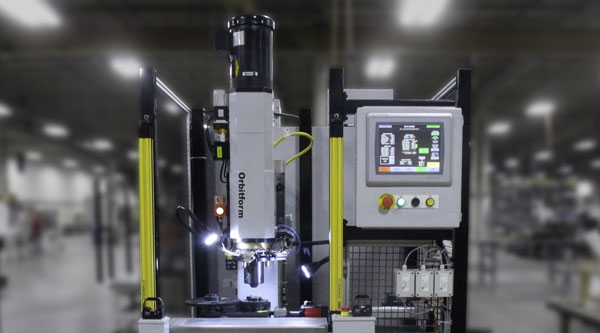
Navigating Machine Configuration
The foundation of effective pivot joint testing lies in comprehending the machine's configuration. A holistic examination entails pivotal elements such as spindle location, clamping mechanisms, part containment strategies, management of rotational friction, and integration of supplementary in-station processes. Each of these facets plays a pivotal role in determining the accuracy and reliability of the testing process.
- Spindle Location: The positioning of the spindle forms a cornerstone in achieving accurate test results. Optimal placement ensures that the torque measurement is not influenced by external factors and accurately reflects the joint's functionality.
- Clamping and Part Containment: The success of the pivot joint testing machine hinges on secure clamping and effective part containment. Achieving this objective primarily relies on the design and implementation of a robust part fixture. Refer to Figure 2 for an illustrative example of the fixture's significance in this context.
- Rotational Friction: Minimizing rotational friction is essential to obtain precise torque measurements. Addressing friction-related concerns ensures that the measured torque values accurately represent the joint's performance.
- In-Station Processes: Beyond the core testing process, integrating other required in-station processes efficiently contributes to a seamless and streamlined production flow.
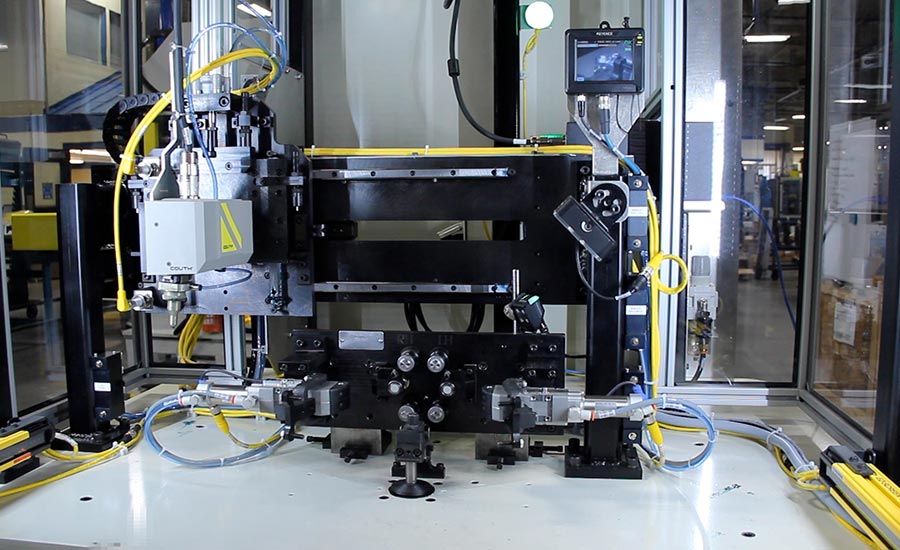
Mastering Part Fixturing
The pivotal role of part fixturing cannot be overstated, particularly in terms of clamping, containment, and facilitating accurate measurements. Delving deeper into the fixture's intricacies, the following considerations come to the fore:
- Support of Rivet/Pivot Joint: The fixture's design should cater to the specific requirements of the rivet or pivot joint, ensuring stability and preventing unwanted movement during testing.
- External Component Locating and Containment: Accurate positioning of external components within the fixture enhances precision and consistency in test results.
- General Fixture Motion: The fixture's motion must be designed to mimic real-world scenarios, enabling a comprehensive evaluation of the joint's functionality.
- Gauging of Motions and Measurements: Implementing precise gauging mechanisms guarantees that the recorded measurements are reliable and reproducible.
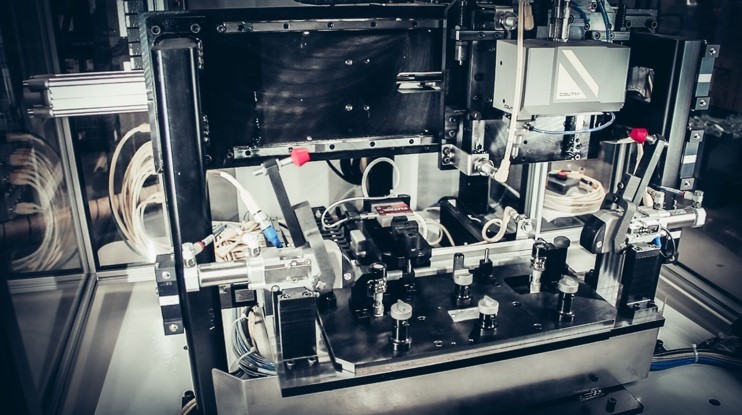
Empowering Control Methodology
The linchpin of a successful pivot joint testing machine lies in its control methodology. This critical aspect is as vital as the well-structured main machine and fixture, as it governs the entire testing process. A careful examination of the control methodology reveals the following considerations:
- Seamless Integration: The control methodology must seamlessly integrate with the machine's mechanics and the fixture's design. A cohesive approach ensures synchronized operation and accurate data acquisition.
- Precision and Consistency: The methodology should enable precise control of variables and guarantee consistent results across multiple tests.
- Real-time Monitoring: Incorporating real-time monitoring and feedback mechanisms enhances the adaptability of the testing process, facilitating prompt adjustments if necessary.
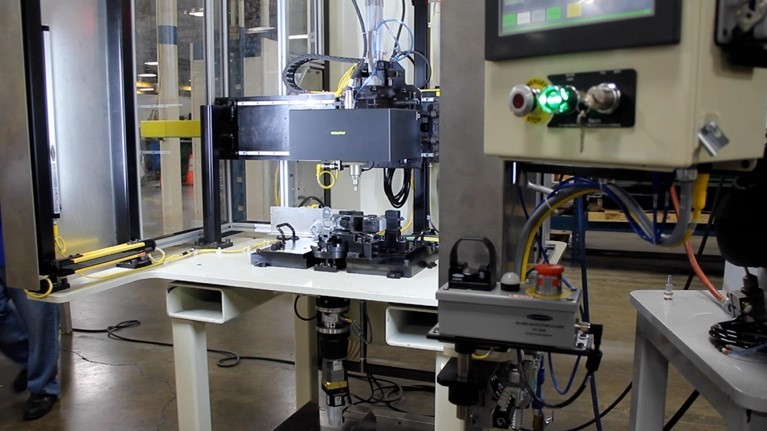
In Conclusion
The realm of pivot joint testing equipment demands meticulous attention to detail across every facet of its construction. The failure to design and configure the machine effectively can lead to disruptions in production flow or render testing efforts futile. As we've explored, the interplay of considerations spanning the main machine, fixture design, gauging and motion verification, and control methodology is pivotal. Only when these components synergize harmoniously can a seamless test sequence be achieved, yielding accurate and irrefutable test data. In an era where quality is paramount, mastering the construction of pivot joint testing equipment is an investment that pays substantial dividends in manufacturing excellence.